How to: Make Your Own InFills
Posted: Fri Jul 03, 2015 11:48 am
How to: Fabricate Your Own In-fills:
For those of us who have done a naked conversion, one big hurdle is figuring out what to do with the area where the coils are mounted. The XJ600N had plastic covers which filled this area in. We commonly refer to those as infills.
What you need:
Here are the what the stock infills looked like:
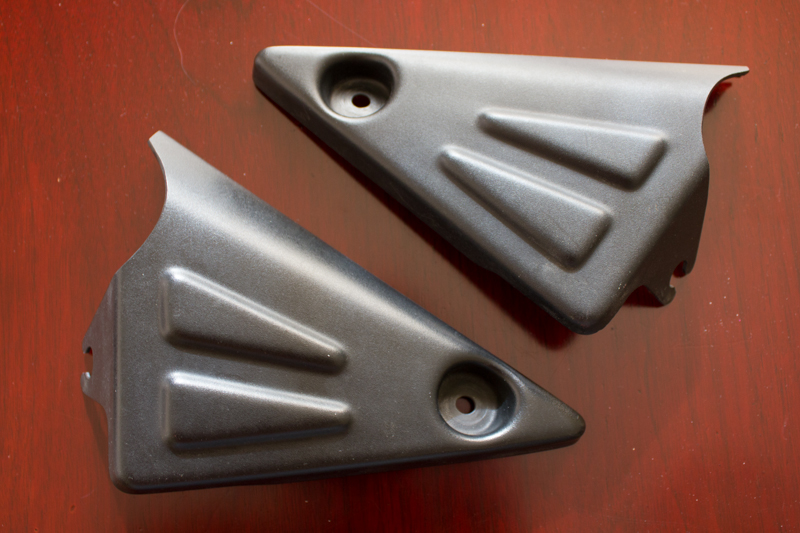
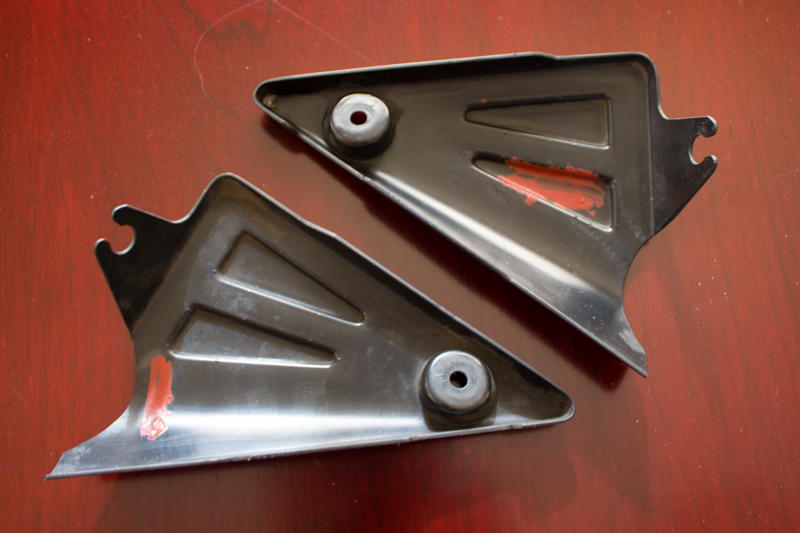
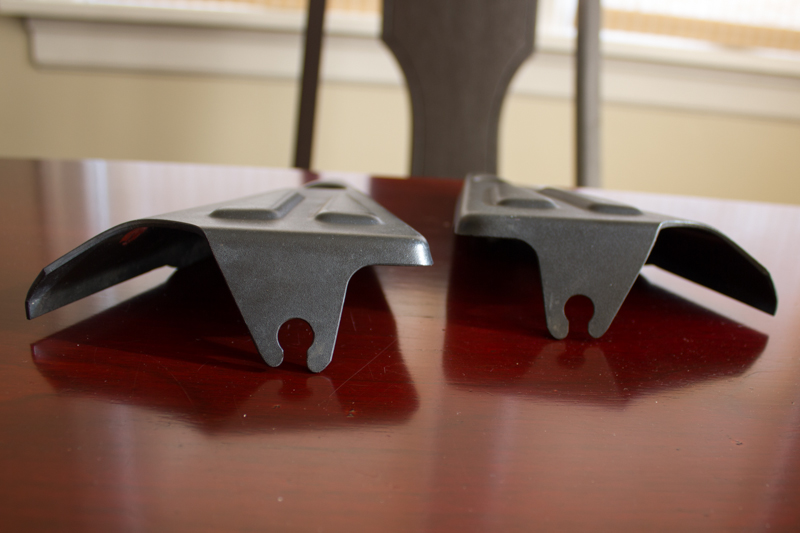
Measurements:
Using those as a basis, here are the measurements & geometry for the left infill (the right one is a mirror image):
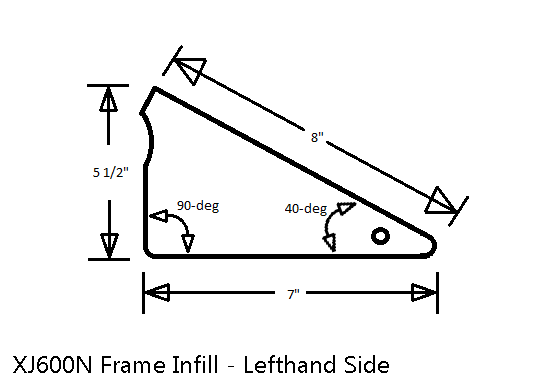
General Approach:
We will be making the new infills out of ABS plastic. ABS plastic is durable, heat resistant, holds paint well and is easy to work with, making it the ideal material for infills. It's also what the rest of your Seca II's body work is made from. The infill will be constructed from four pieces, the main body and three edges, giving it a 3-dimensional shape.
Make a pattern:
Make yourself a pattern out of cardboard, using the previously listed measurements. Verify that this pattern fits by holding it up to the bike and confirming clearances. Trim the pattern as needed.
Cut your ABS:
Lay the pattern onto the ABS plastic and trace it with a Sharpie marker. Using a band saw or other appropriate saw, cut out the main infill section. Once cut, clean up the edges with some sandpaper; I used my Dremel. Take the infill out to the bike and ensure it fits the way you want to.
Once you have the main section cut out, make the edges. I used my table saw, with the fence set 1" from the edge of the blade. I ripped the ABS sheet into three pieces and then cut those to length using the chop saw.
Here are the ABS pieces I used to make one infill:
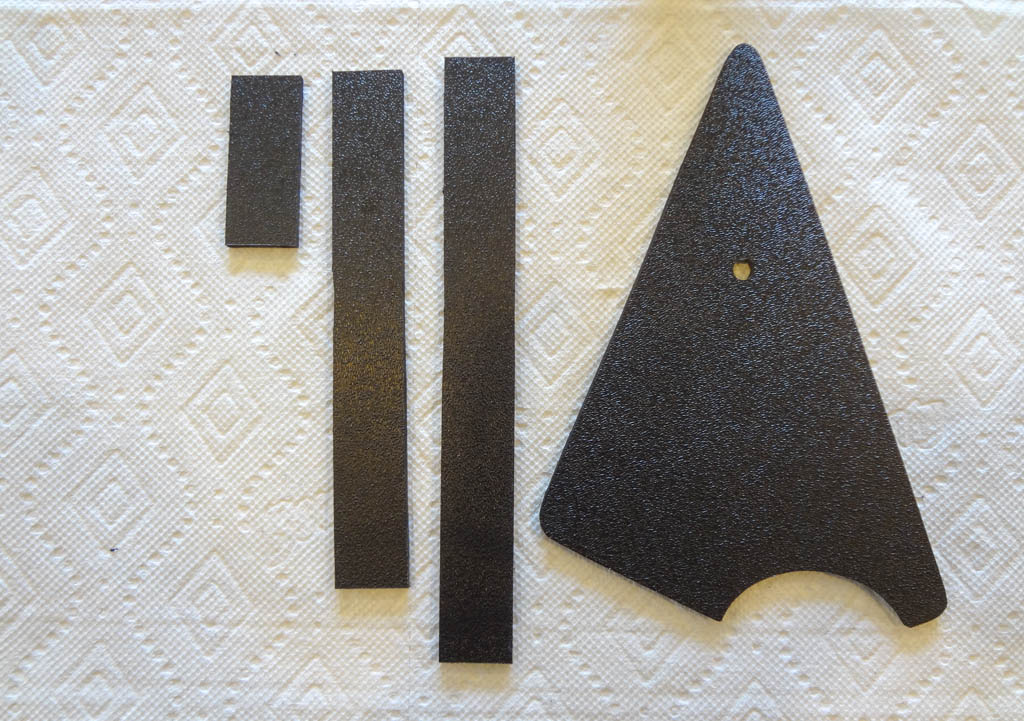
Once the ABS pieces are cut, ensure they are clean and remove any abs burrs that remain. The edges should be flat and clean.
Glue your infill together:
Apply a liberal coating of ABS cement to the edge of the first ABS side piece and place it on the main piece. Hold it in place firmly, for 30 seconds. Do the same thing with the second edge piece and glue it in place. Be sure to apply ABS cement to the edge where they join.
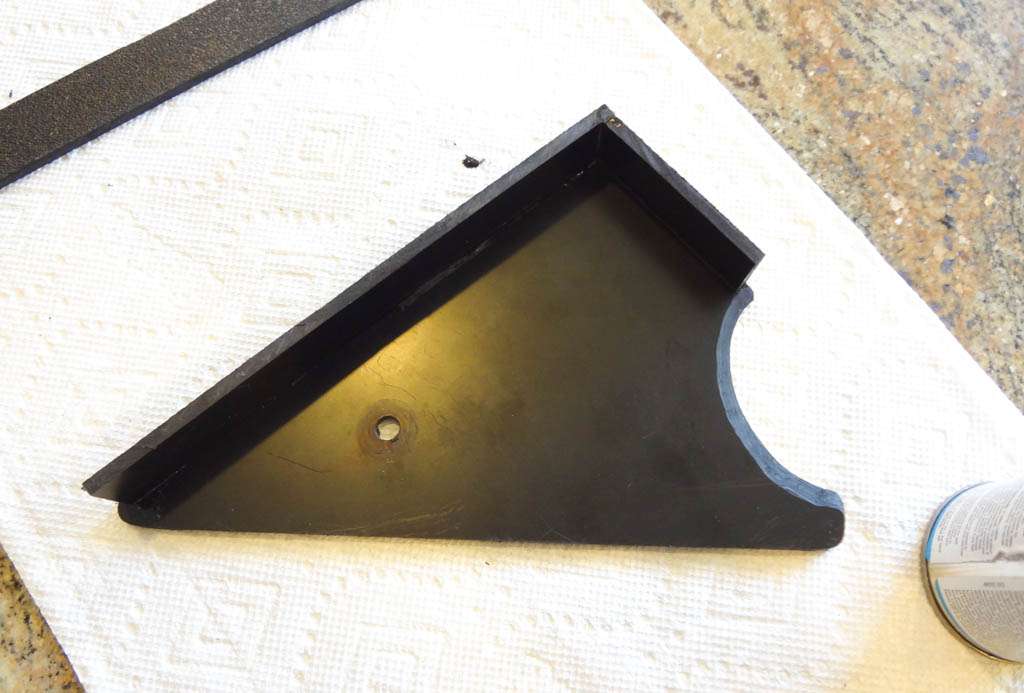
Continue the same process with the last edge piece. Knowing that the top-edge would be visible and wanting a smooth seam, I left extra material that will be sanded off in a later step. This is only really necessary on the top most side piece:
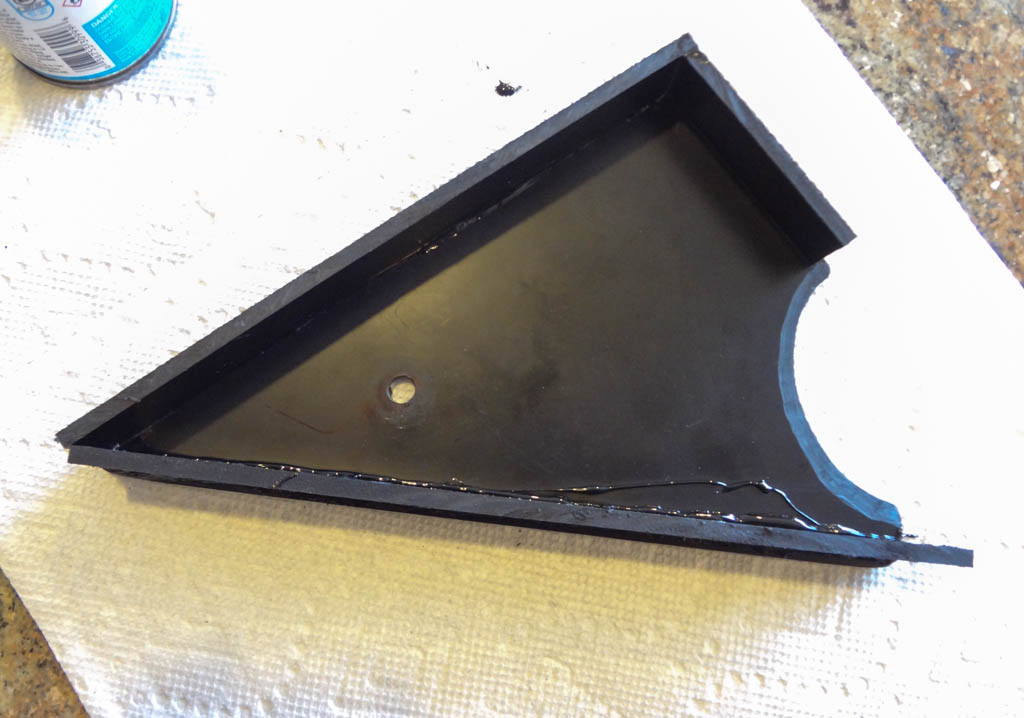
Finish the gluing by adding a coat along the internal edge of the infill. This will add some strength to the joint and will ensure it's consistently bonded:
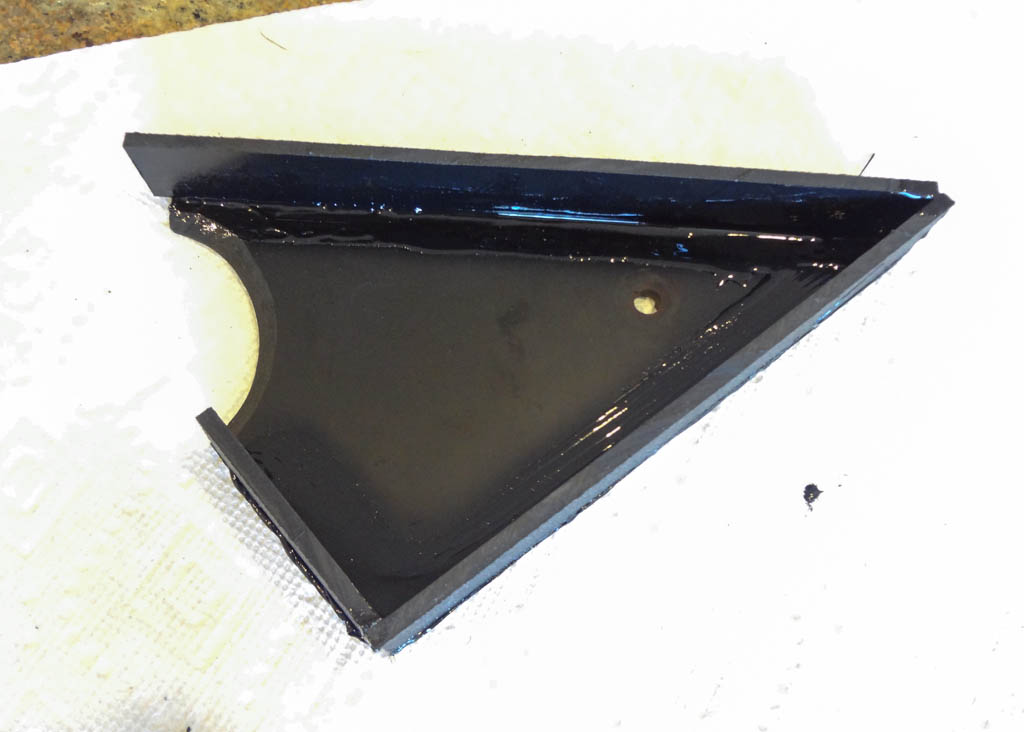
Repeat the same processes for the other infill. Here are my two infills, side-by-side:
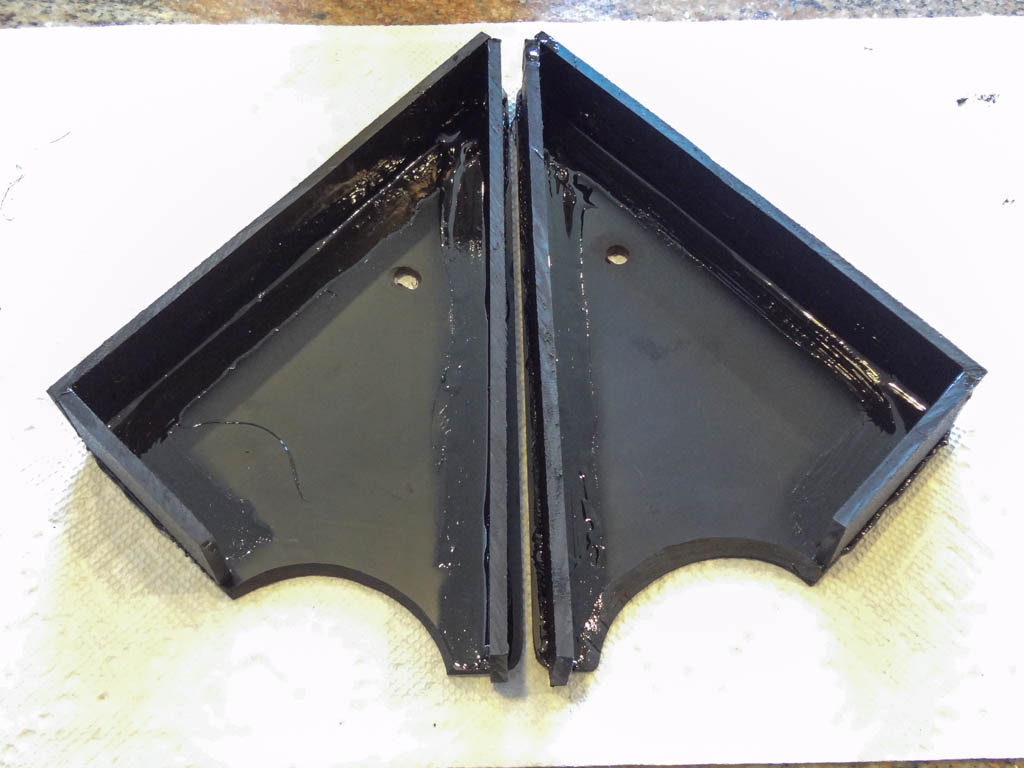
Let them dry:
Leave the infills alone. Walk away. Let them dry for a minimum of 24 hours before trying to fit them, move them or sand them.
Sand/Shape your infills:
Use a sanding wheel mounted in your drill press or Dremel to sand and shape the infills. I used a Dremel tool with a 1/2" sanding disk to sand the edges of the infill smooth and to contour them. Here's mine after shaping:
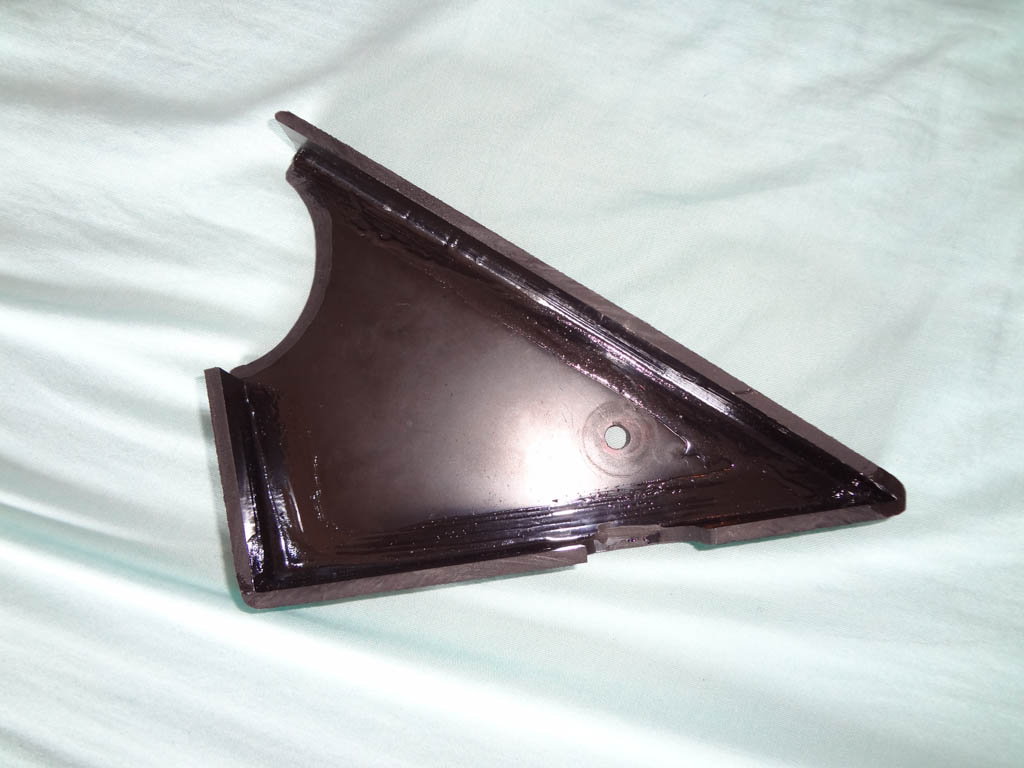
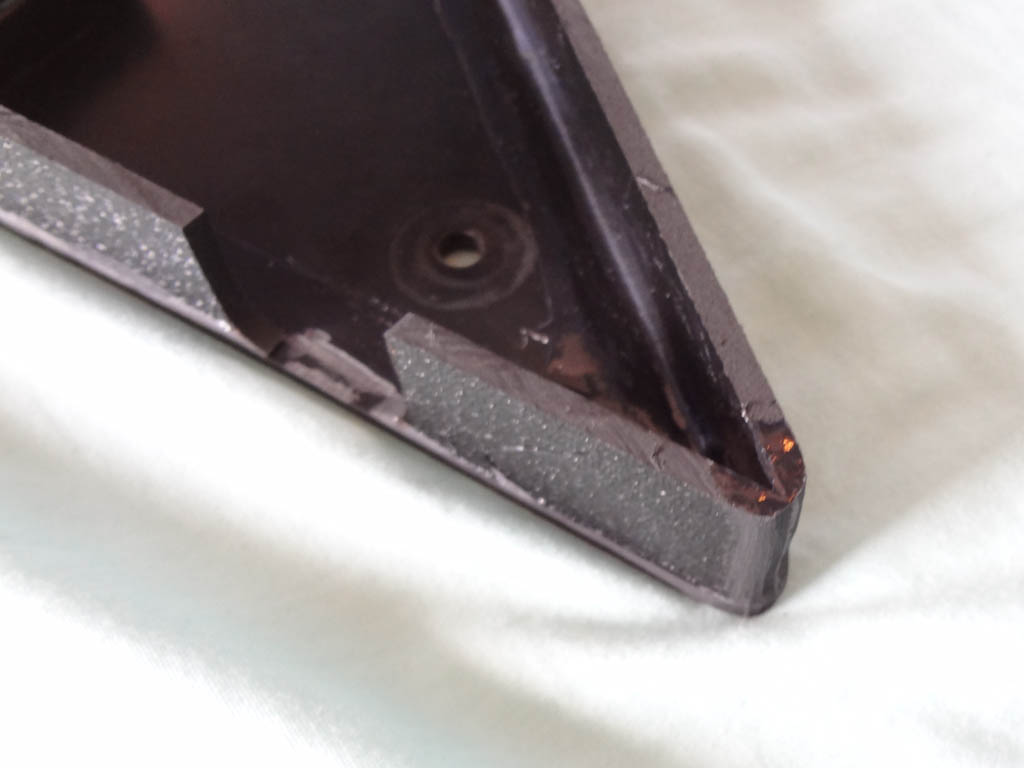
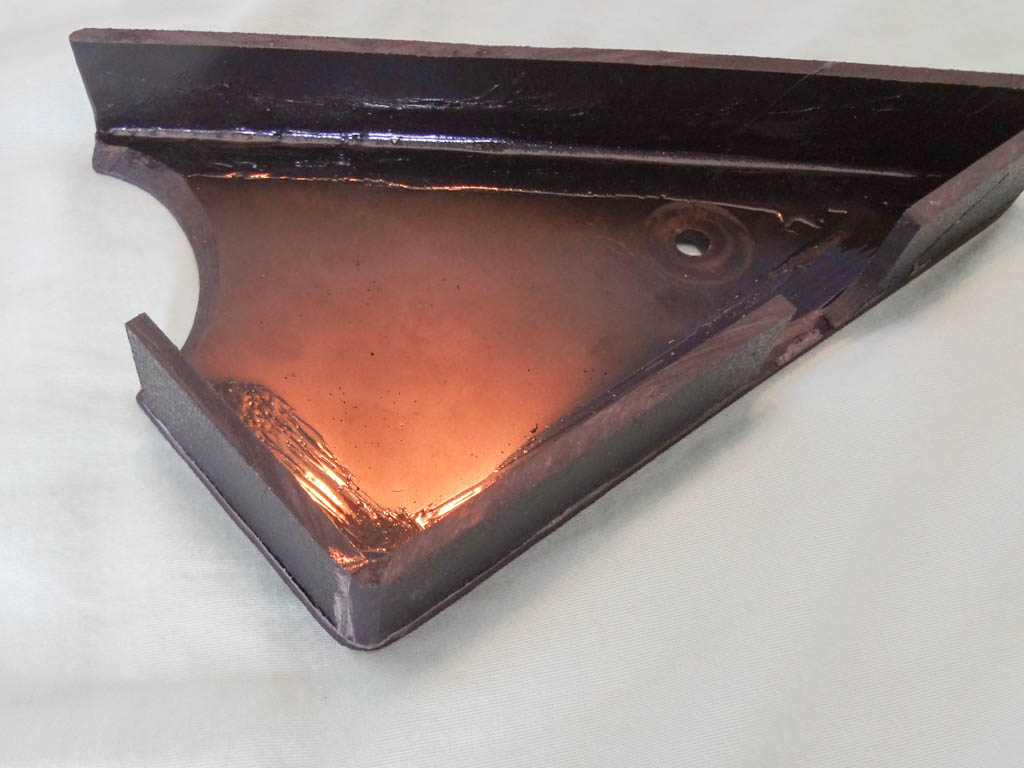
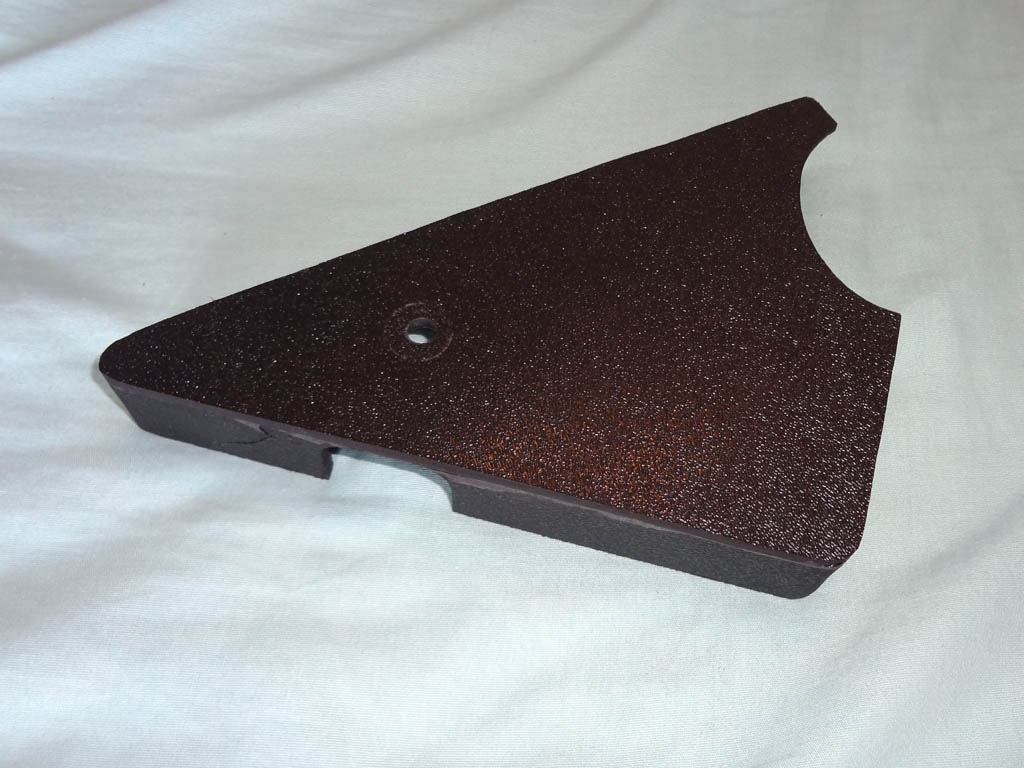
To sand the infills smooth, I used 120-grit sandpaper in my Mouse sander (palm sander). I sanded the edges smooth and then sanded off the texture. I finished by rounding the edges to soften the appearance of the infills. Here's the results:
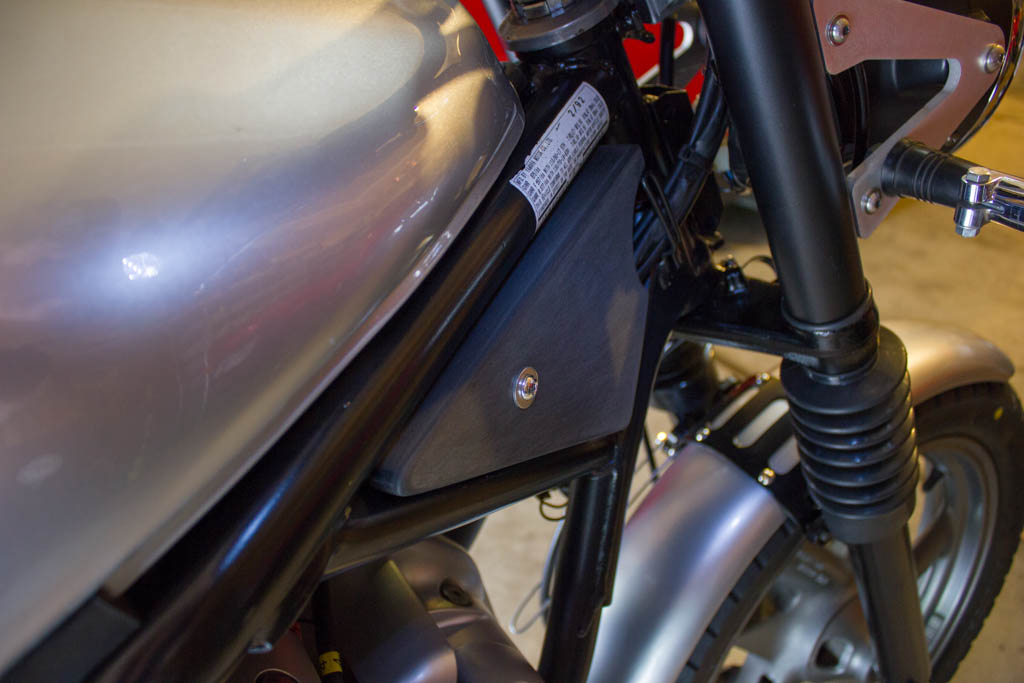
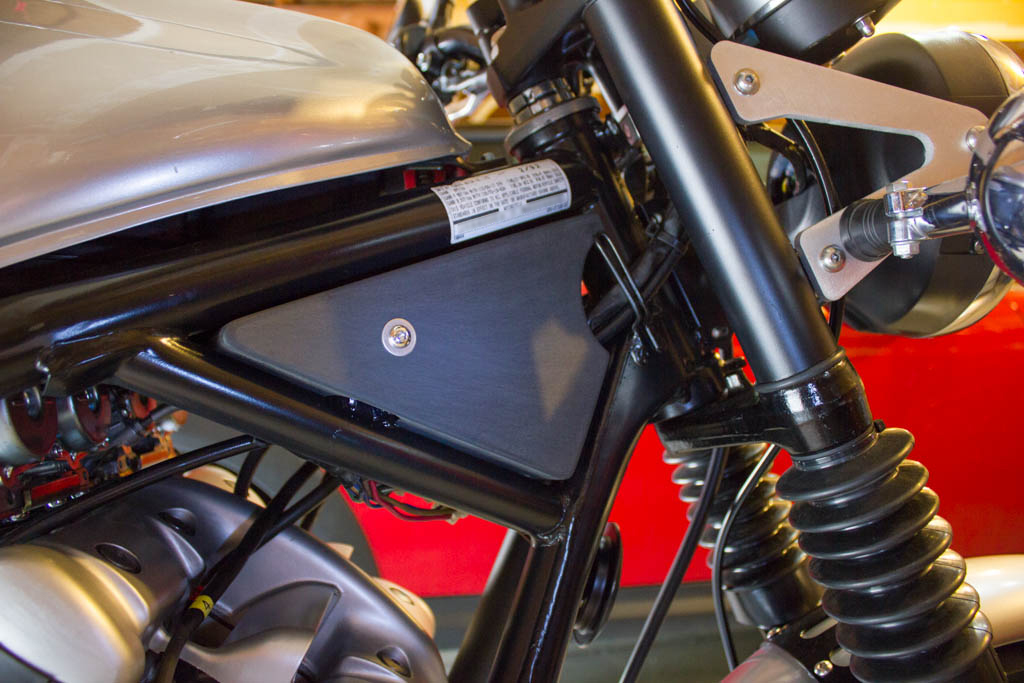
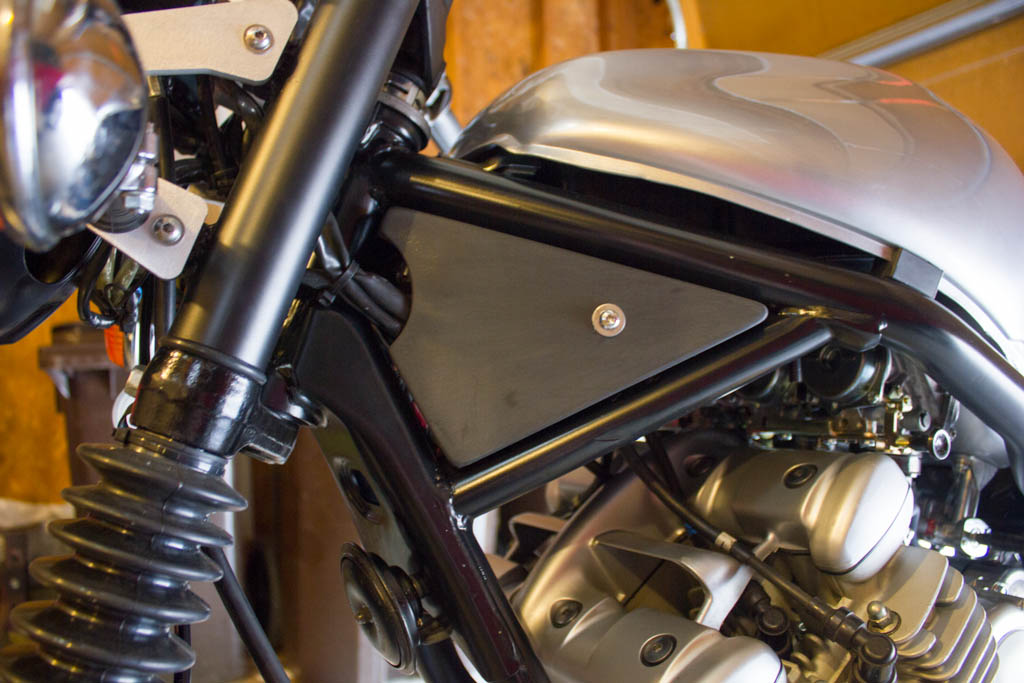
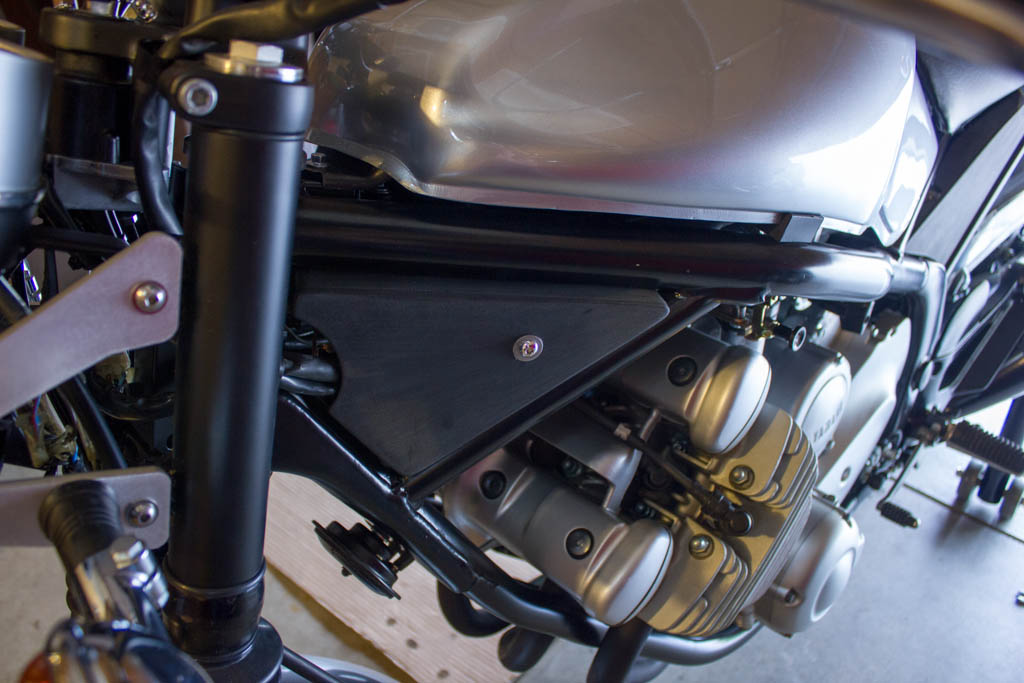
Add Detail to your infills:
If you wish to have additional raised detail or other shaps, cut them out of additional ABS plastic and glue to them to the face of your infills. As an example, a pair of triangles could be cut and adhered to match the stock infills.
Install your infills:
I attached my infills to my frame using a welded-on tab with a well-nut installed. On my black/red bike, they are attached using a band clamp and a bracket. Here's the mounting solution for these infills. Welded-tab with a well-nut.
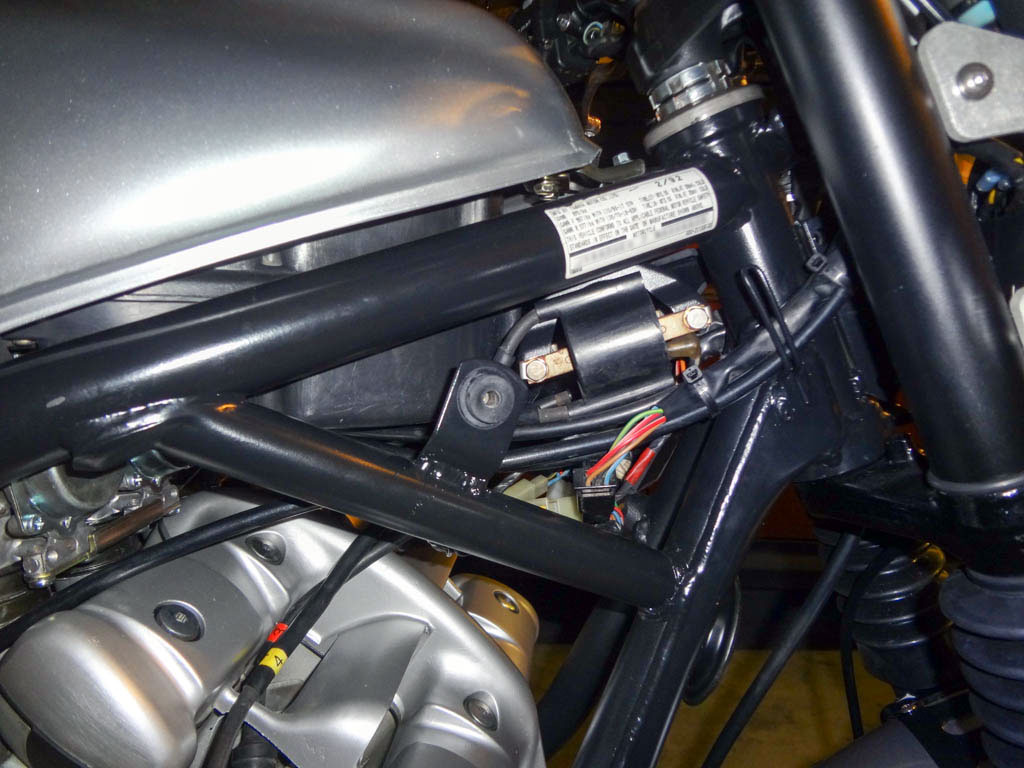
Finished Product:
Here are the infills, installed.
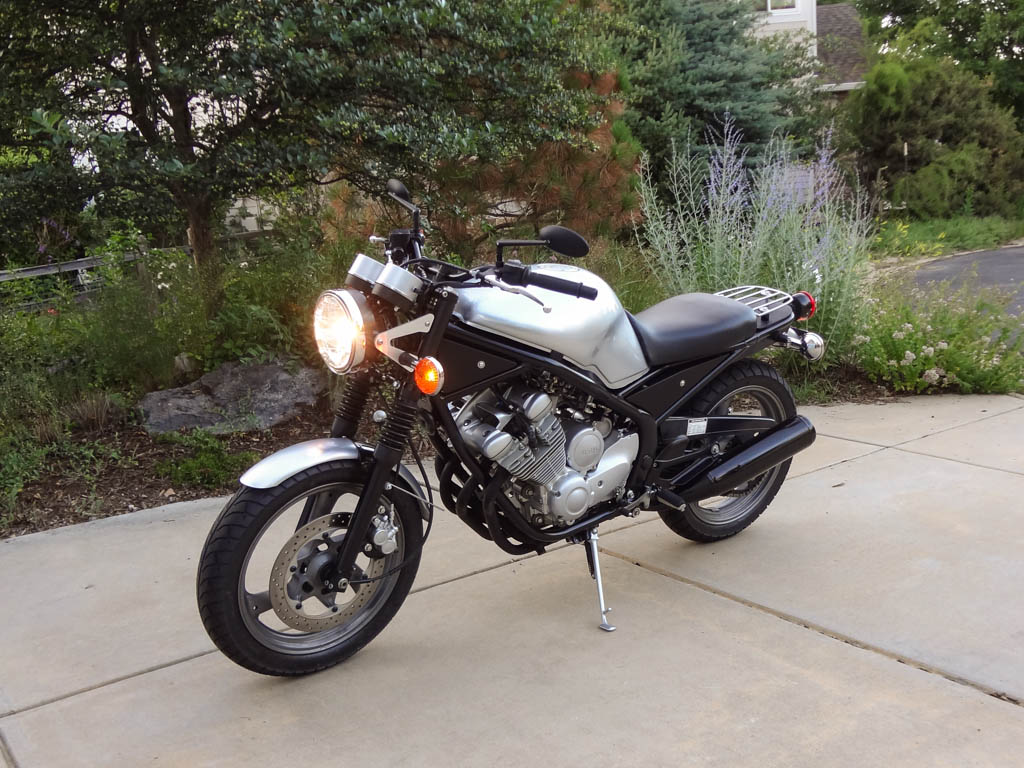
For those of us who have done a naked conversion, one big hurdle is figuring out what to do with the area where the coils are mounted. The XJ600N had plastic covers which filled this area in. We commonly refer to those as infills.
What you need:
- Two (2) sheets of 3/16" thick ABS plastic. I bought mine on EBay.
- One (1) can of ABS glue. This absolutely has to be ABS glue and not a general purpose glue. ABS glue is black in color, smells of acetone and is available in your local hardware store's plumbing section. This is a must!
- Tools for cutting ABS plastic. I used a band-saw, table saw and chop saw typically used for carpentry. Anything that can cut wood should work for cutting the plastic.
- Tools for sanding ABS plastic. I used a sanding wheel in my Dremel for sanding/shaping the plastic and a Mouse sander to sound the surfaces smooth. I finished with wet-or-dry sandpaper.
Here are the what the stock infills looked like:
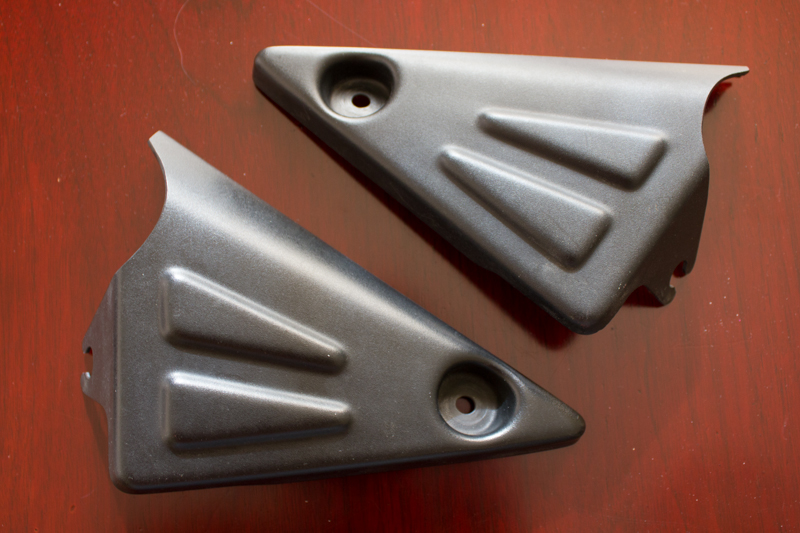
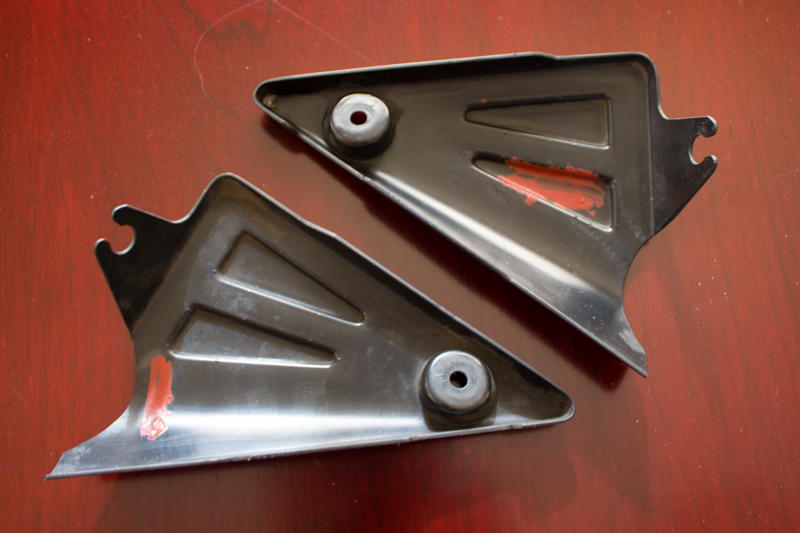
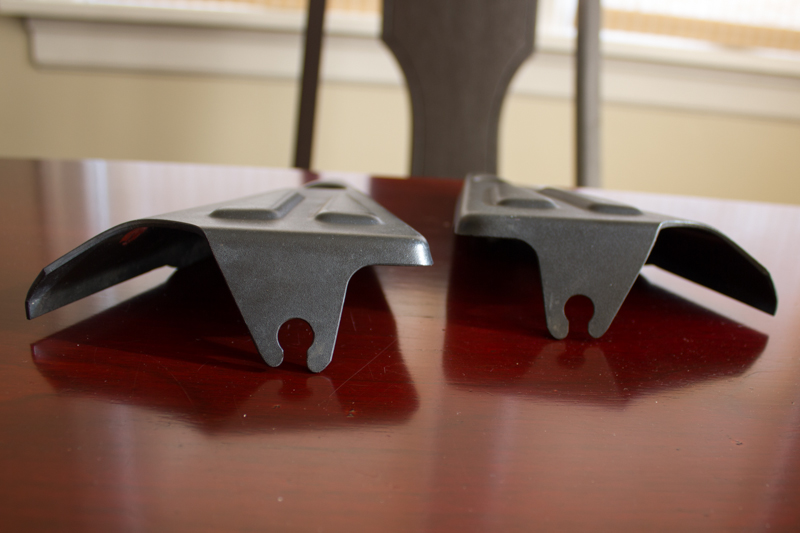
Measurements:
Using those as a basis, here are the measurements & geometry for the left infill (the right one is a mirror image):
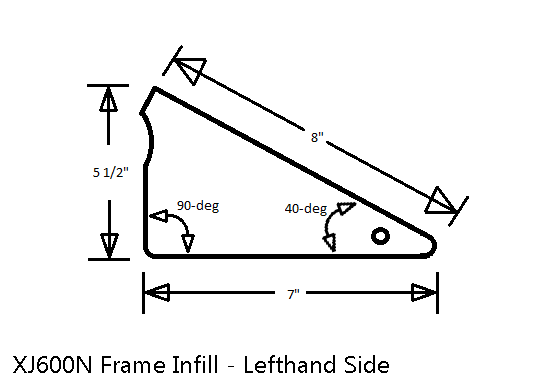
General Approach:
We will be making the new infills out of ABS plastic. ABS plastic is durable, heat resistant, holds paint well and is easy to work with, making it the ideal material for infills. It's also what the rest of your Seca II's body work is made from. The infill will be constructed from four pieces, the main body and three edges, giving it a 3-dimensional shape.
Make a pattern:
Make yourself a pattern out of cardboard, using the previously listed measurements. Verify that this pattern fits by holding it up to the bike and confirming clearances. Trim the pattern as needed.
Cut your ABS:
Lay the pattern onto the ABS plastic and trace it with a Sharpie marker. Using a band saw or other appropriate saw, cut out the main infill section. Once cut, clean up the edges with some sandpaper; I used my Dremel. Take the infill out to the bike and ensure it fits the way you want to.
Once you have the main section cut out, make the edges. I used my table saw, with the fence set 1" from the edge of the blade. I ripped the ABS sheet into three pieces and then cut those to length using the chop saw.
Here are the ABS pieces I used to make one infill:
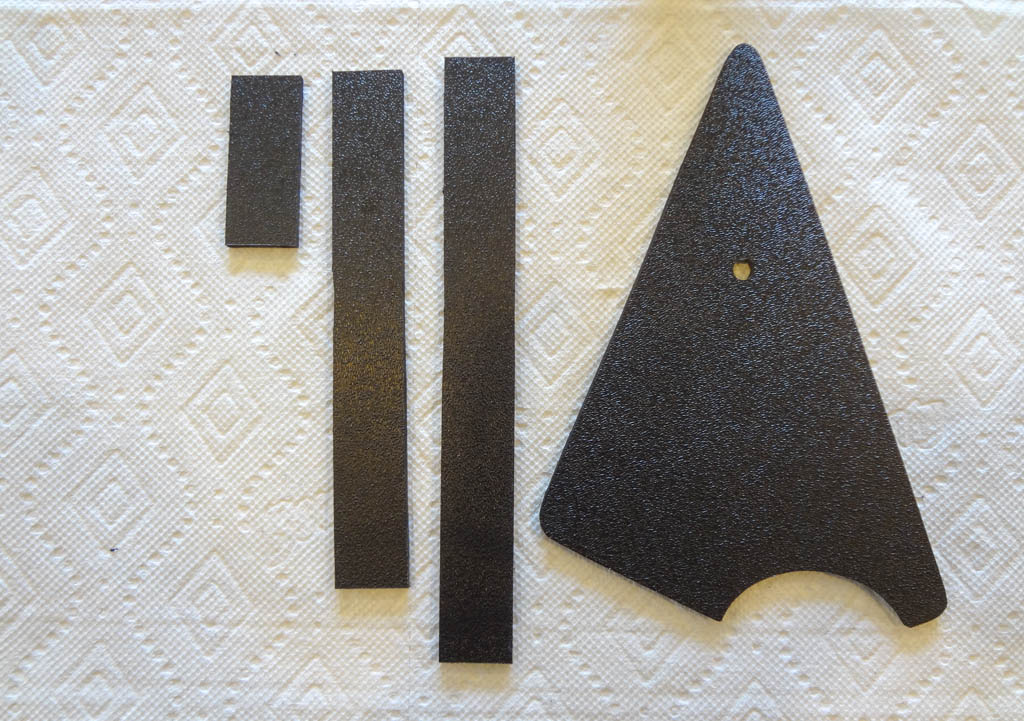
Once the ABS pieces are cut, ensure they are clean and remove any abs burrs that remain. The edges should be flat and clean.
Glue your infill together:
Apply a liberal coating of ABS cement to the edge of the first ABS side piece and place it on the main piece. Hold it in place firmly, for 30 seconds. Do the same thing with the second edge piece and glue it in place. Be sure to apply ABS cement to the edge where they join.
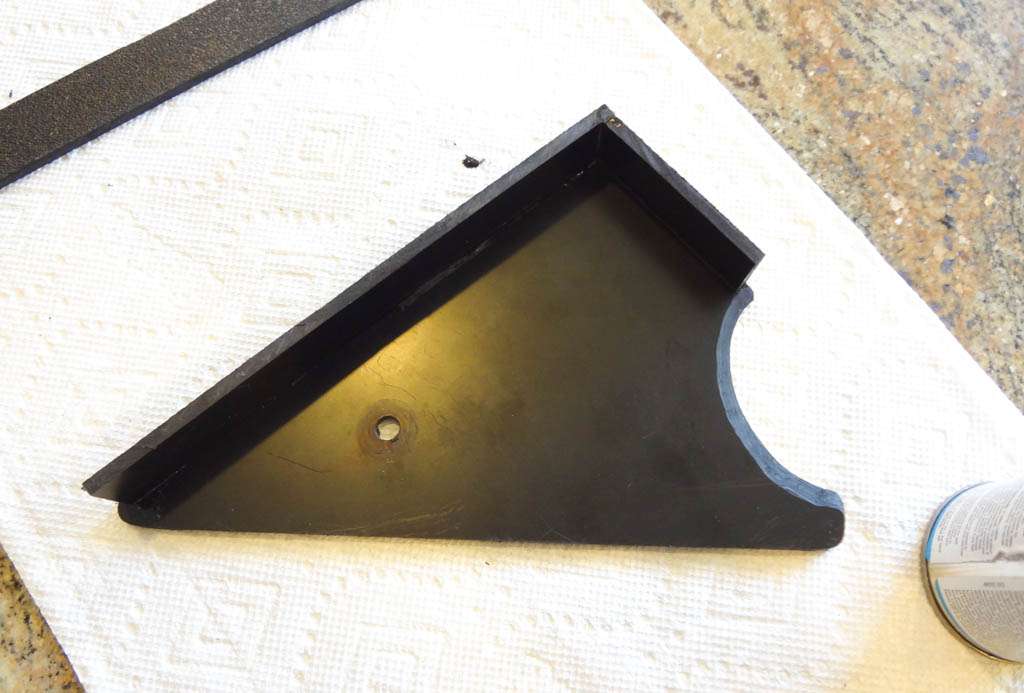
Continue the same process with the last edge piece. Knowing that the top-edge would be visible and wanting a smooth seam, I left extra material that will be sanded off in a later step. This is only really necessary on the top most side piece:
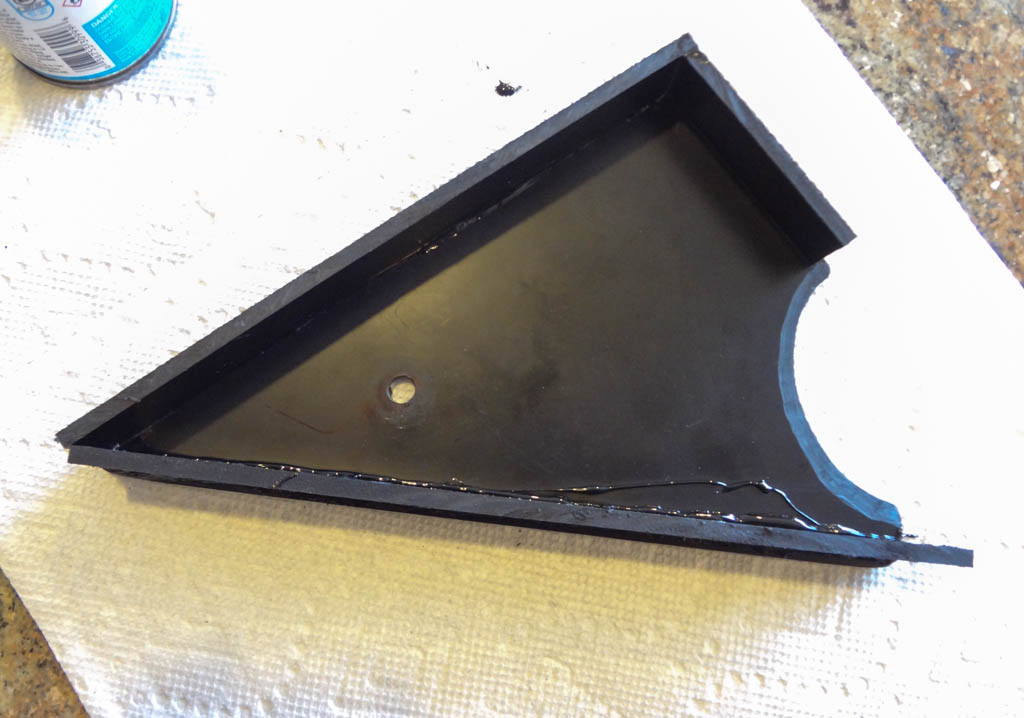
Finish the gluing by adding a coat along the internal edge of the infill. This will add some strength to the joint and will ensure it's consistently bonded:
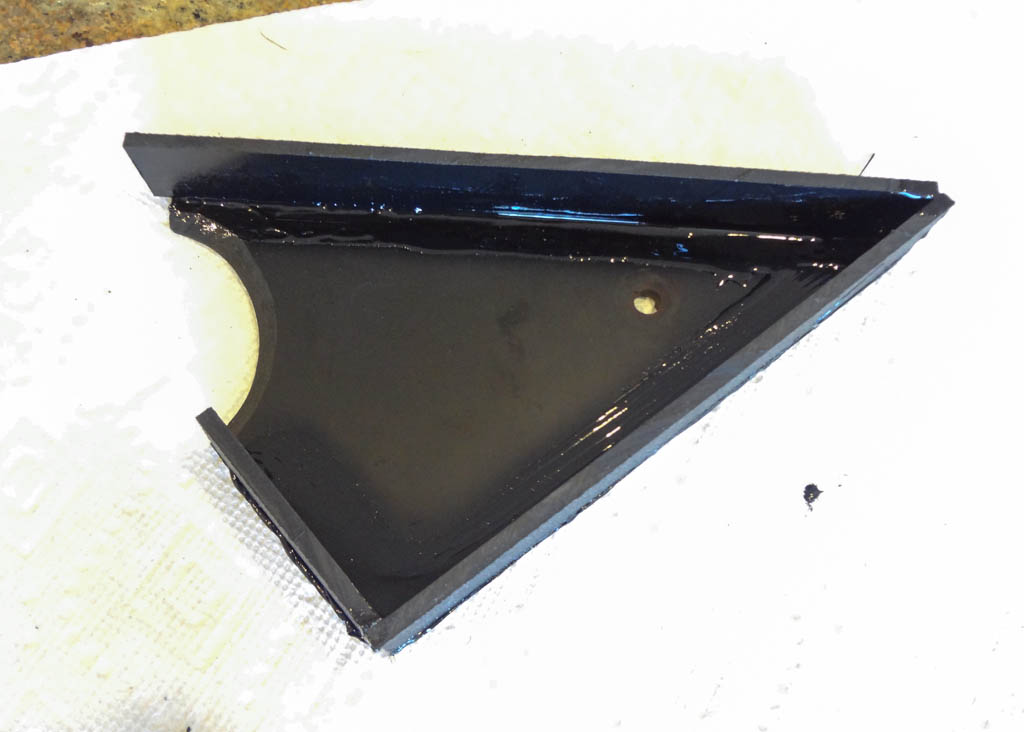
Repeat the same processes for the other infill. Here are my two infills, side-by-side:
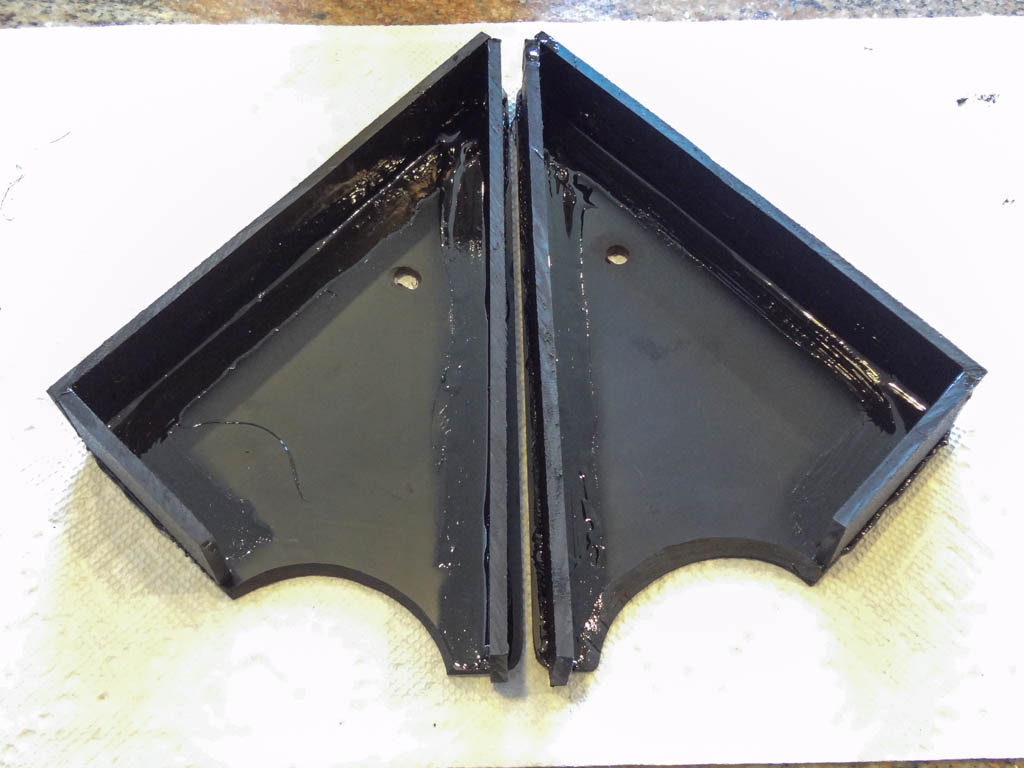
Let them dry:
Leave the infills alone. Walk away. Let them dry for a minimum of 24 hours before trying to fit them, move them or sand them.
Sand/Shape your infills:
Use a sanding wheel mounted in your drill press or Dremel to sand and shape the infills. I used a Dremel tool with a 1/2" sanding disk to sand the edges of the infill smooth and to contour them. Here's mine after shaping:
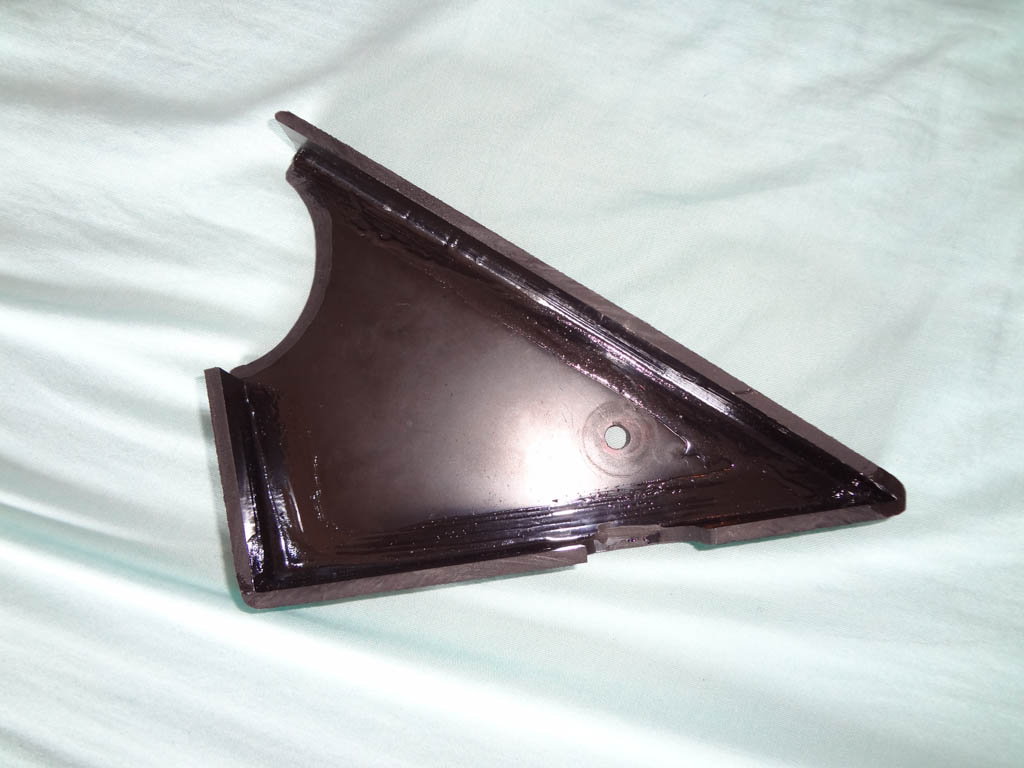
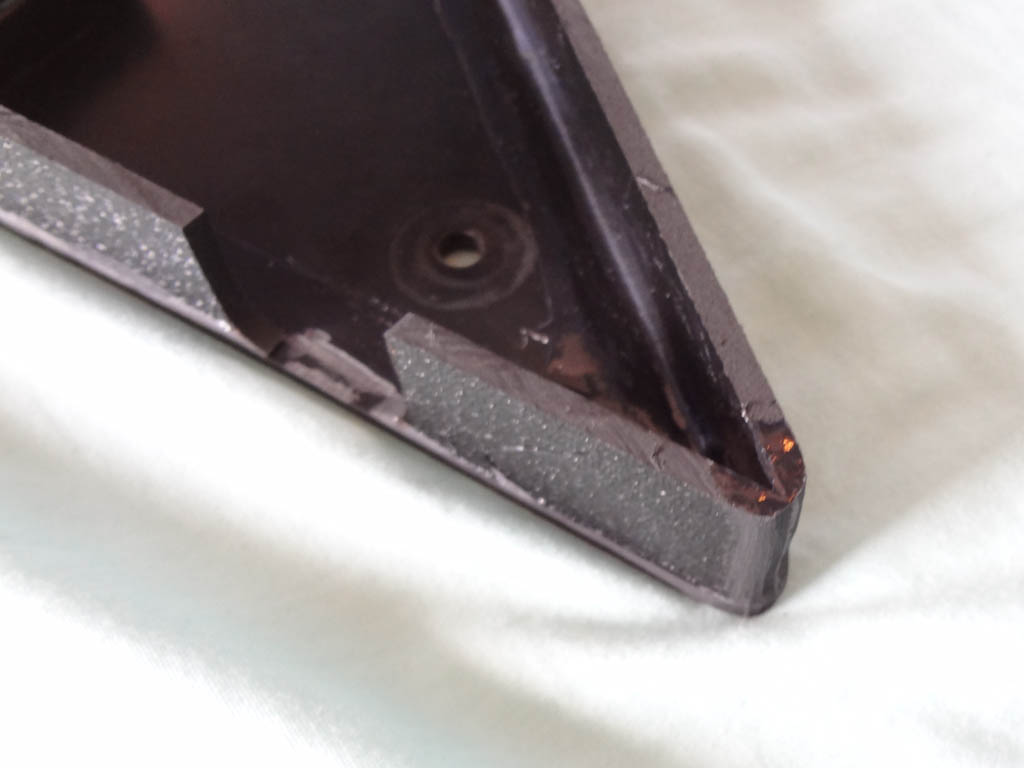
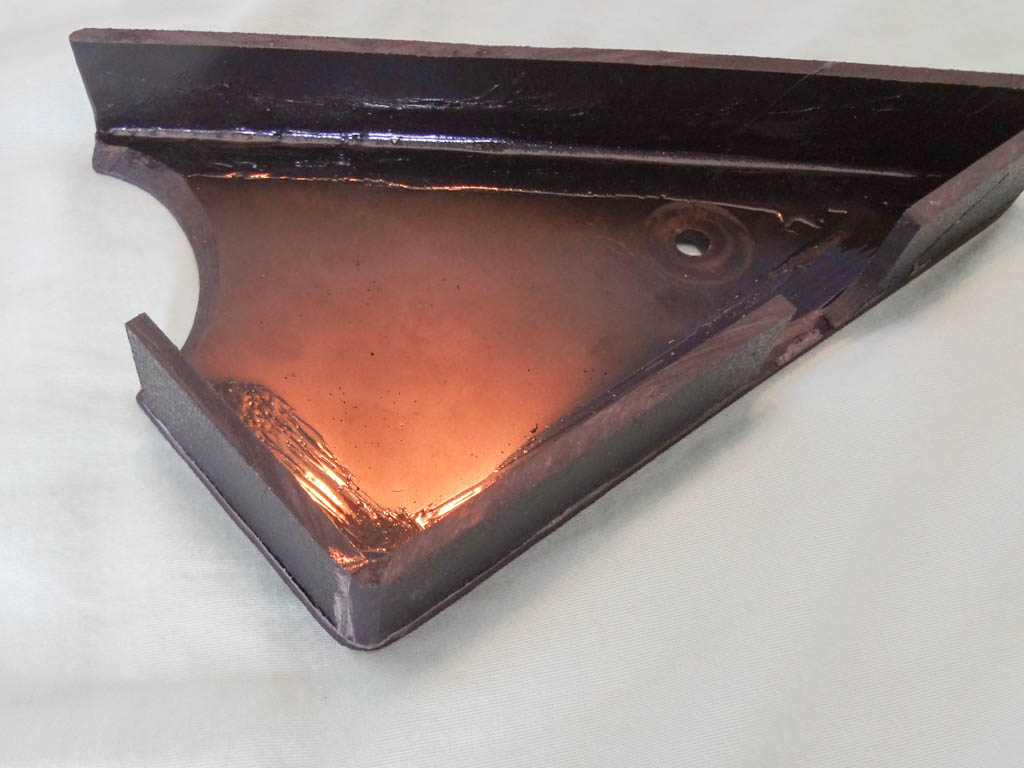
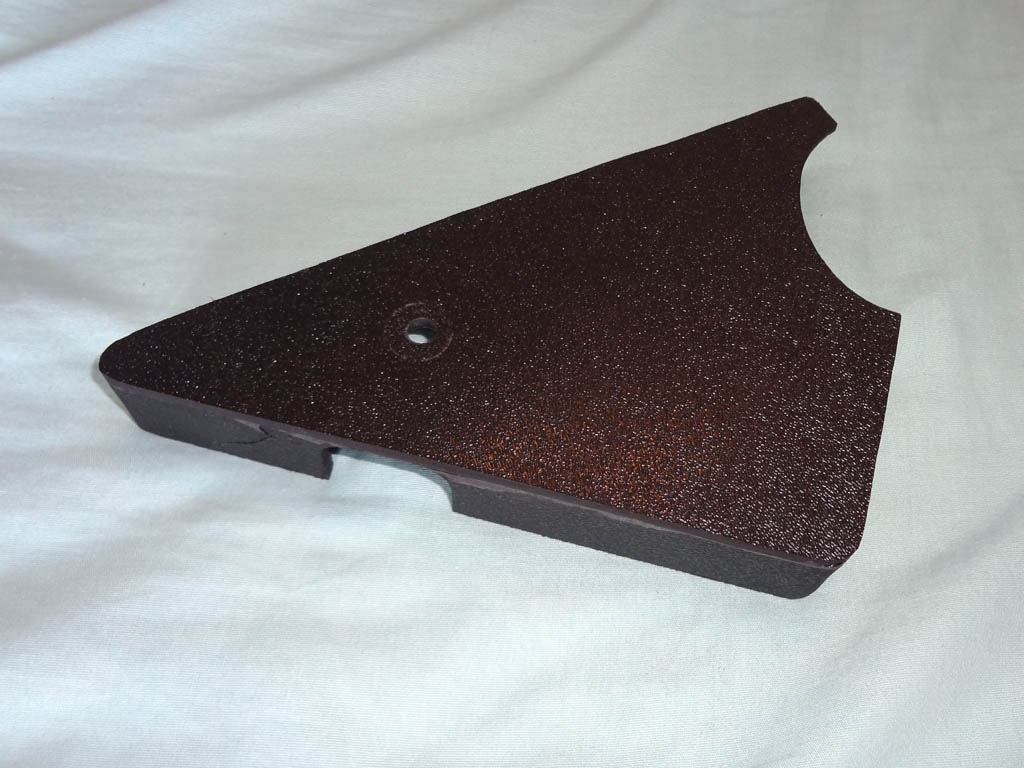
To sand the infills smooth, I used 120-grit sandpaper in my Mouse sander (palm sander). I sanded the edges smooth and then sanded off the texture. I finished by rounding the edges to soften the appearance of the infills. Here's the results:
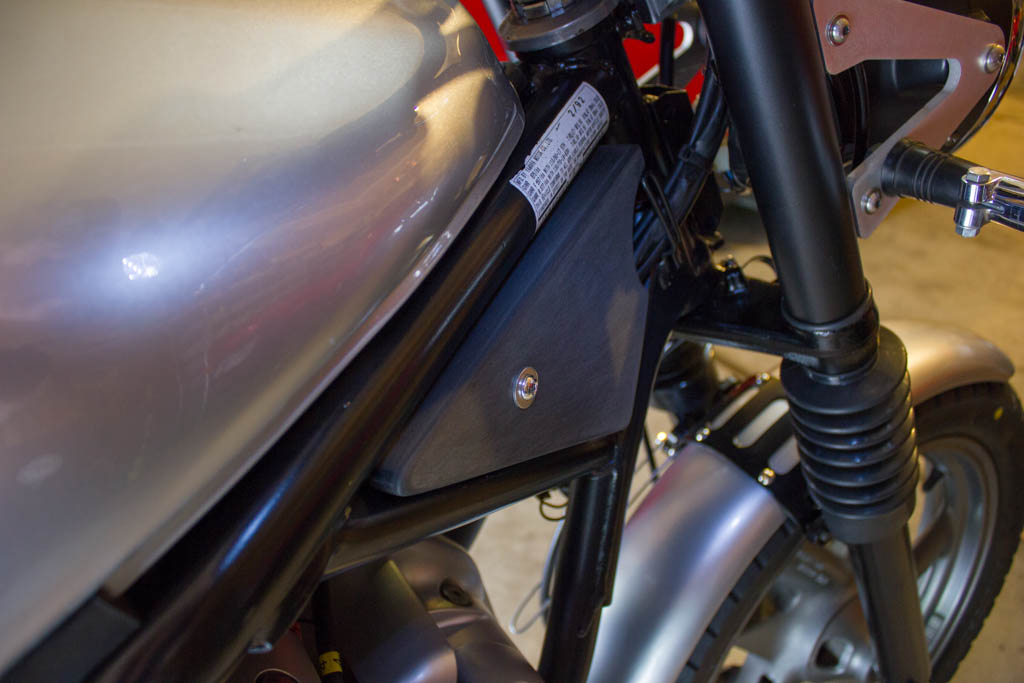
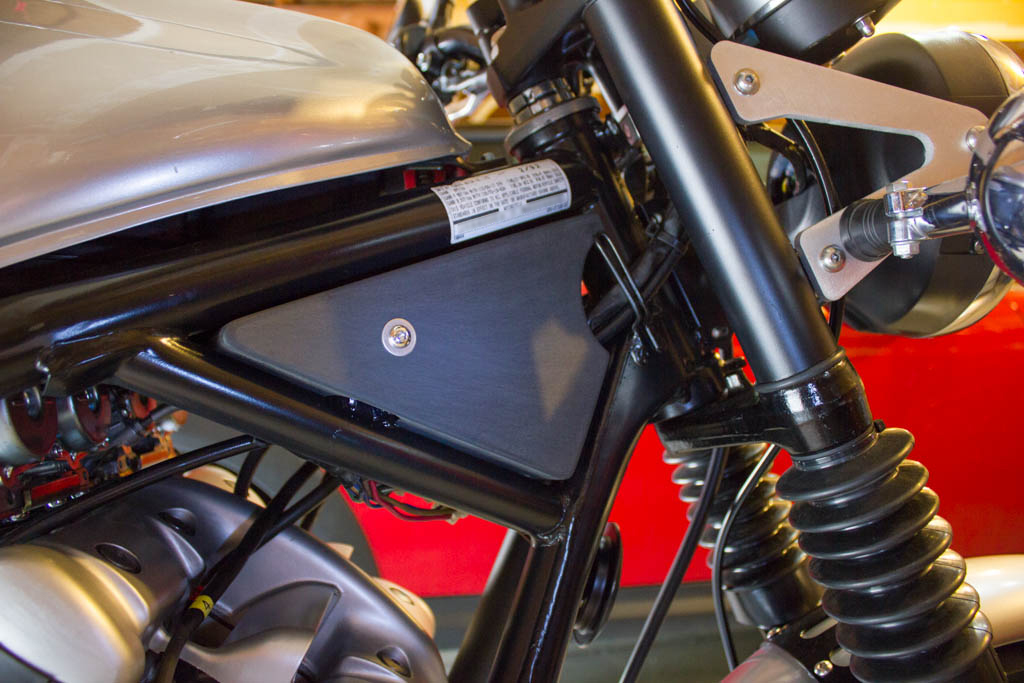
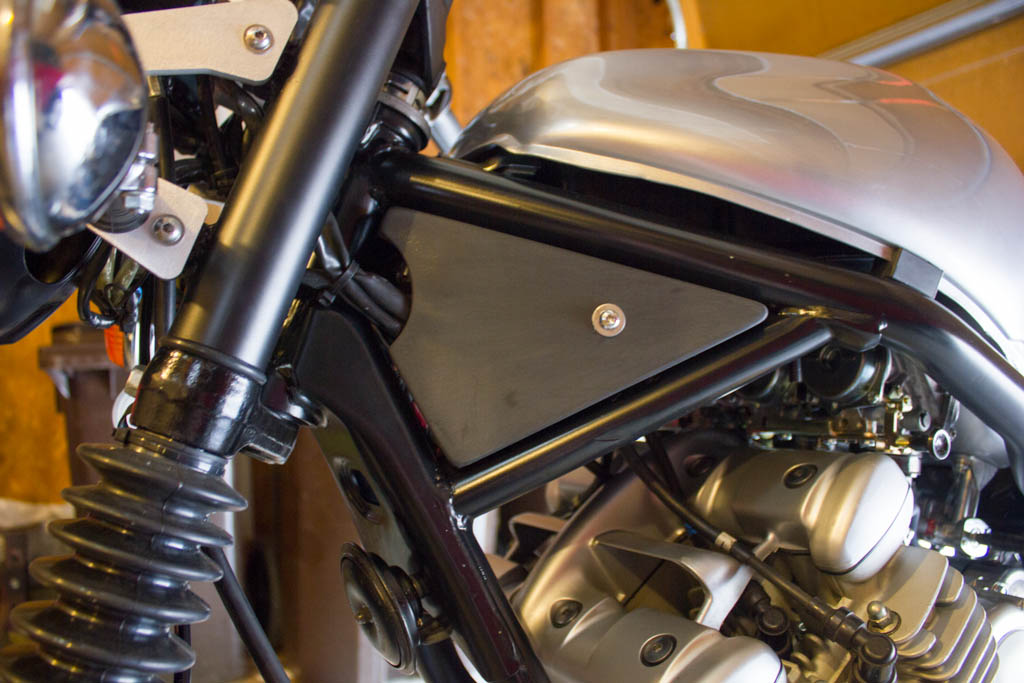
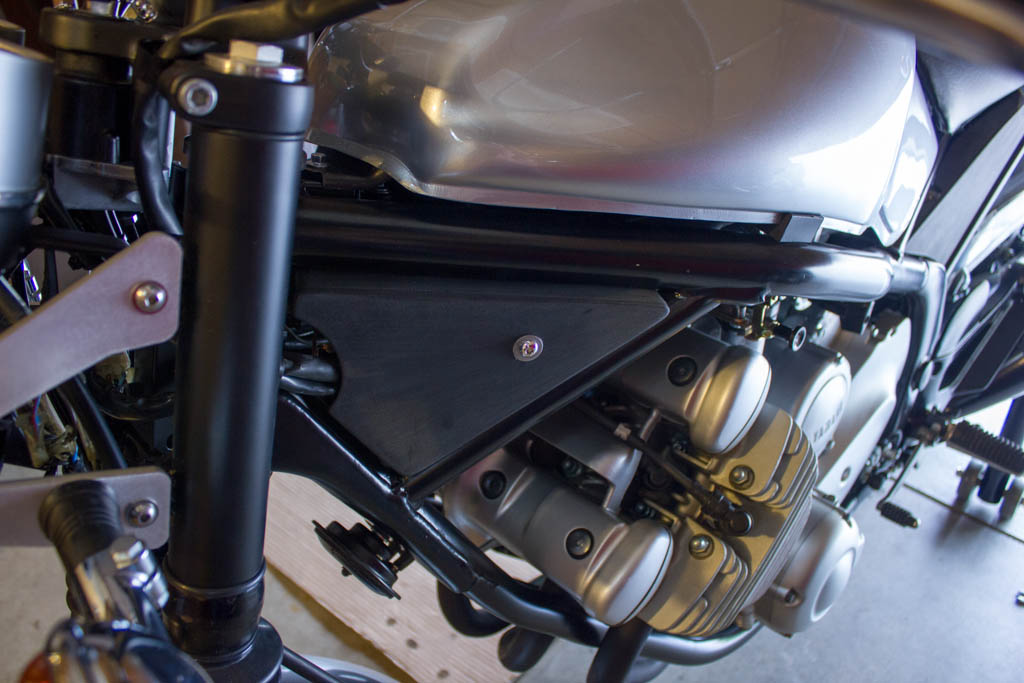
Add Detail to your infills:
If you wish to have additional raised detail or other shaps, cut them out of additional ABS plastic and glue to them to the face of your infills. As an example, a pair of triangles could be cut and adhered to match the stock infills.
Install your infills:
I attached my infills to my frame using a welded-on tab with a well-nut installed. On my black/red bike, they are attached using a band clamp and a bracket. Here's the mounting solution for these infills. Welded-tab with a well-nut.
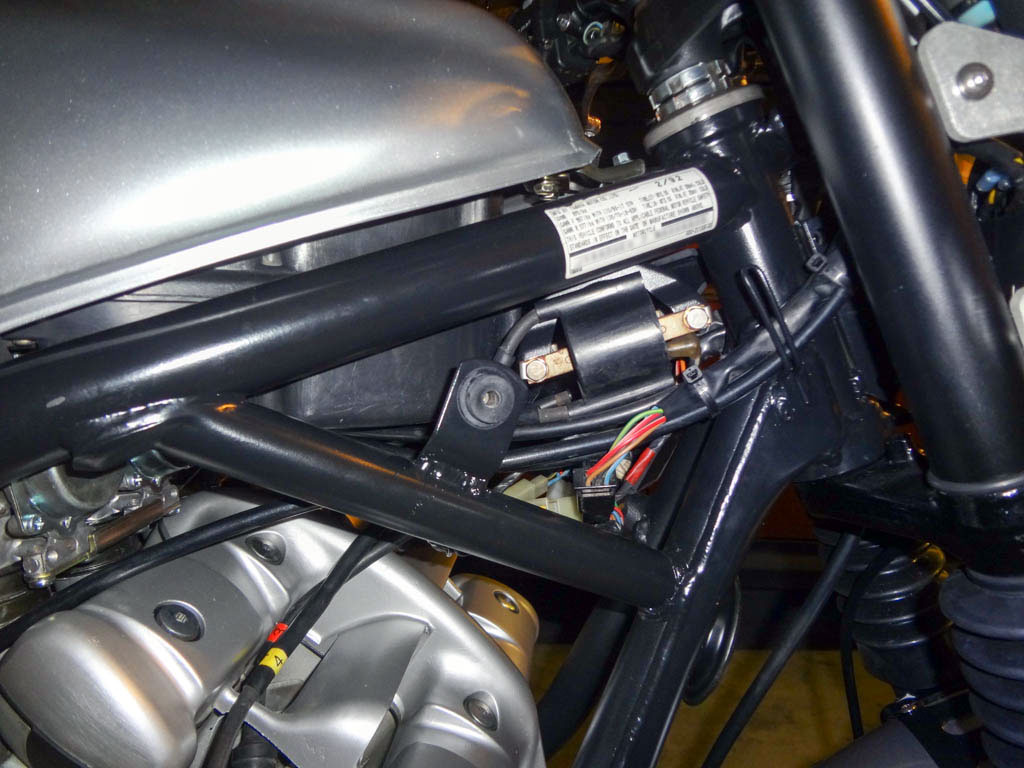
Finished Product:
Here are the infills, installed.
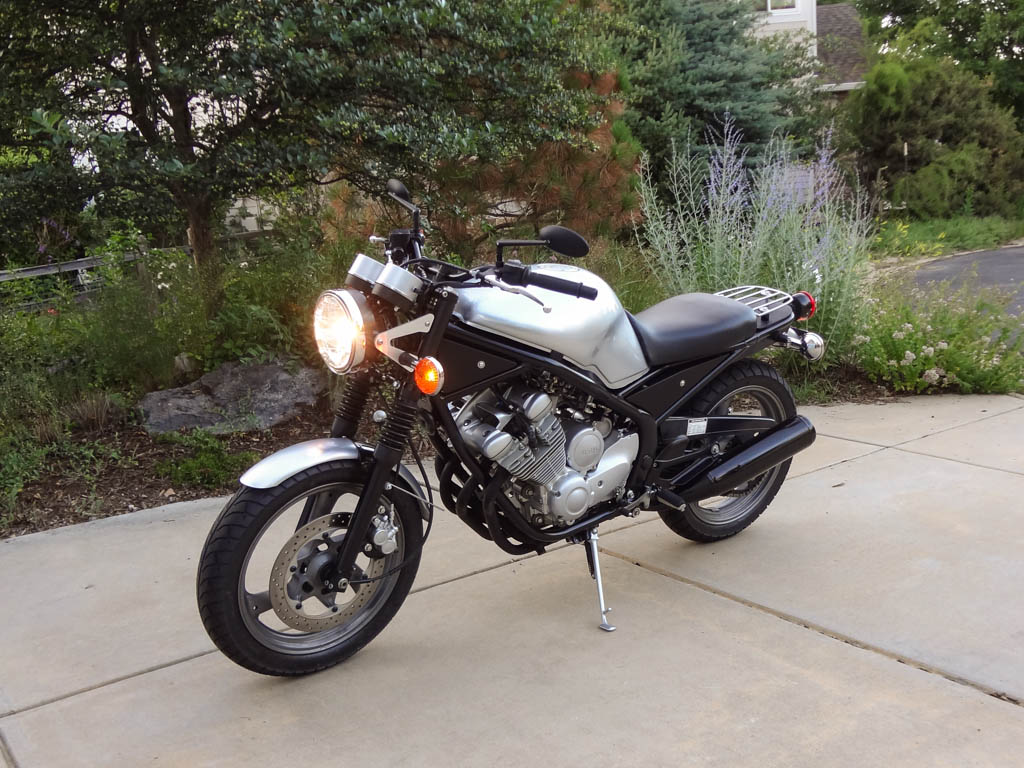